UAV Manoeuvrability Analysis
✅ Paper Type: Free Essay | ✅ Subject: Aviation |
✅ Wordcount: 2014 words | ✅ Published: 23 Sep 2019 |
Introduction to UAV Manoeuvrability
Unmanned Aerial Vehicles (UAVs) have transformed the way we approach surveillance, mapping, and transport. Their manoeuvrability is a key factor in their effectiveness. Modern UAVs, including drones and hybrid airships, offer unique advantages over traditional aircraft. They require less power, can hover, and often operate with greater precision. However, their performance depends on design, stability, and the environments in which they fly.
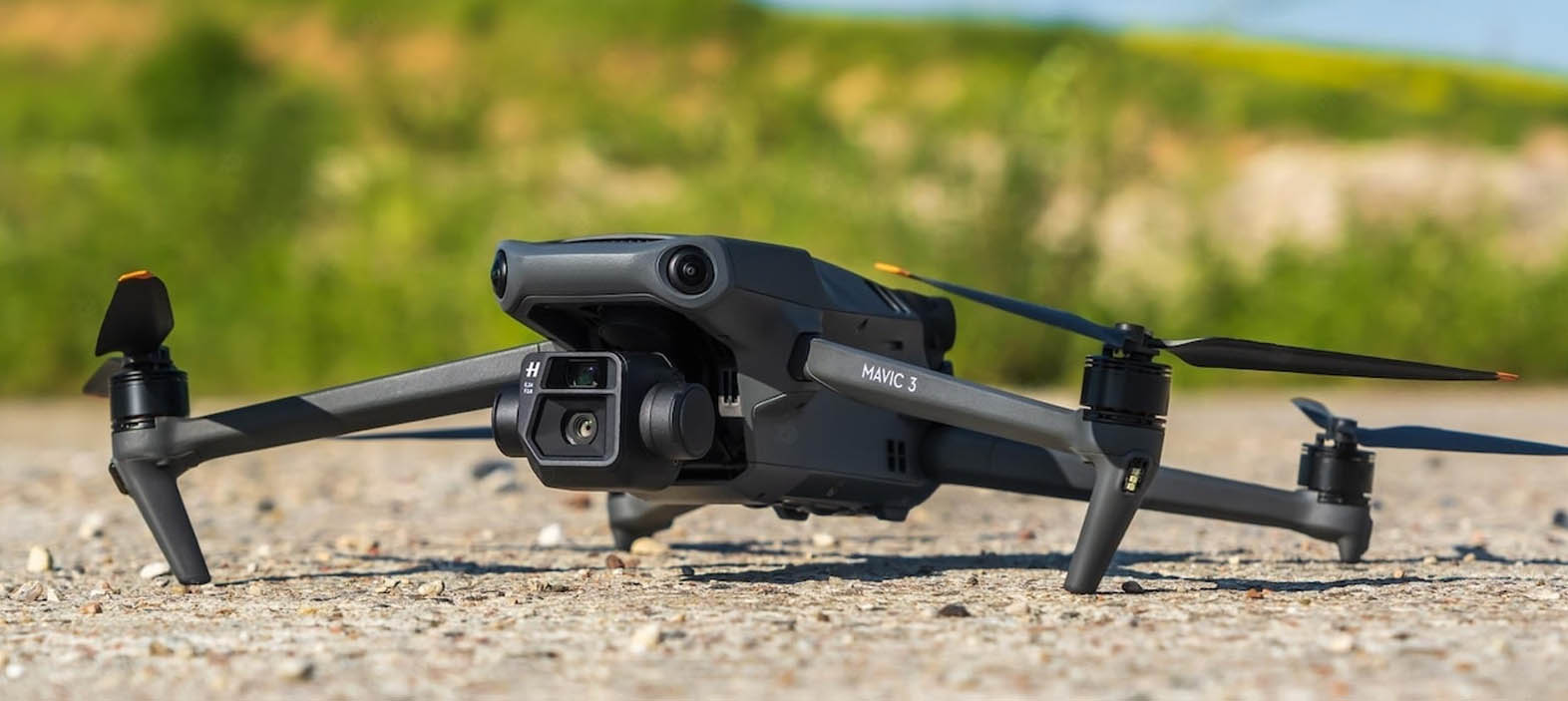
UAVs have evolved rapidly in recent years. Designers now blend the strengths of different aircraft types to create hybrid models. These hybrids combine buoyancy-driven lift with aerodynamic lift from wings. This approach addresses many stability issues found in older airship designs. As a result, UAVs can now handle more complex missions, even in challenging weather conditions.
This article explores the factors that influence UAV manoeuvrability. It compares modern UAVs with traditional airships and highlights the latest advances in design and materials. You will also find links to further reading, including related articles on UKessays.com.
The Evolution of UAVs and Airships
UAVs have a rich history. Early lighter-than-air vehicles, such as hot air balloons, date back to the late 18th century. The Montgolfier brothers launched the first hot air balloon in 1783. Soon after, Jean Pilatre de Rozier made the first manned flight. These early balloons relied on buoyancy, but they lacked control and manoeuvrability.
Rigid airships, like the famous Zeppelins, appeared in the early 20th century. These airships used metal frameworks to maintain their shape and carried passengers across continents. However, accidents such as the Hindenburg disaster in 1937 led to a decline in their use. Despite setbacks, research into lighter-than-air technology continued, especially for military and research purposes.
Today, UAVs are used for a wide range of missions. They support advertising, tourism, research, and even disaster response. Designers now focus on improving manoeuvrability, efficiency, and safety. Hybrid airships, which combine buoyancy and aerodynamic lift, are at the forefront of this innovation.
Modern UAV Designs and Configurations
UAVs come in many shapes and sizes. At their core, they must meet two main requirements. First, they need to withstand aerodynamic and propulsion loads. Second, their envelopes must be streamlined to reduce drag.
Conventional UAVs
Traditional UAVs and airships fall into two main categories: blimps (pressure airships) and rigid airships. Blimps maintain their shape through internal gas pressure. They are simple to build but can struggle with stability. Rigid airships use a framework to support their shape. This allows for larger sizes and more complex payloads.
Semi-rigid airships combine the best features of both types. They use a partial framework to handle bending loads without adding much weight. This makes them easier to build and operate.
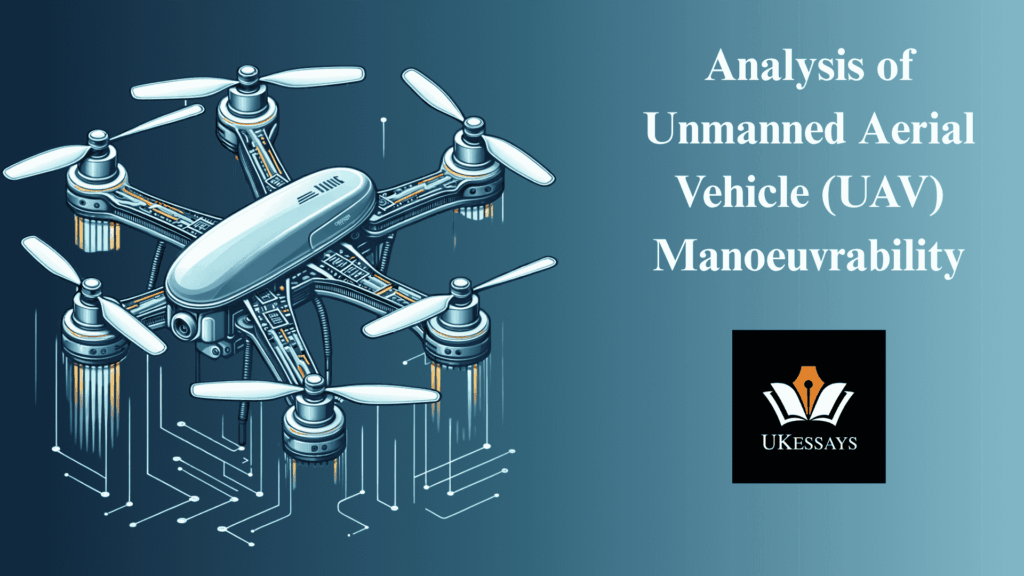
Unconventional and Hybrid UAVs
Hybrid UAVs represent the latest step in design evolution. These vehicles combine features from aeroplanes and helicopters with traditional airships. For example, some hybrids use wings to generate extra lift. Others use vectored propellers to improve thrust and control.
These designs allow UAVs to take off and land with less runway. They also improve ground handling and stability. By mixing technologies, engineers can tailor UAVs for specific missions. For example, a hybrid UAV might use buoyancy for endurance and wings for speed.
Many recent studies have explored these configurations. They show that adding wings or vectored thrust can greatly improve manoeuvrability. For example, a V-shaped airship with two propellers can achieve better control in yaw, roll, and pitch than a traditional teardrop-shaped model.
Aerostatic and Aerodynamic Principles
Understanding UAV manoeuvrability starts with the basics of aerostatics and aerodynamics. The lift generated by a UAV depends on the volume of its gasbag and the density difference between the lifting gas and the surrounding air.
Buoyancy and Lift
The buoyancy force acts upward on a body immersed in air. The net lift is the difference between this force and the total weight of the UAV. The total weight includes the envelope, the lifting gas, and any payload.
As a UAV ascends, the air pressure drops. This causes the gasbag to expand. However, temperature also falls, which increases gas density. The balance between pressure and temperature determines the maximum altitude, known as the “pressure height.” At this point, the gasbag is fully inflated, and further ascent reduces lift.
Designers must carefully manage the inflation fraction of the gasbag. If it is too high at sea level, the UAV cannot ascend without losing lift. The goal is to maximise lift while maintaining structural integrity.
Lifting Gases
Most UAVs use helium as their lifting gas. Helium is non-flammable and safe to handle. Hydrogen offers more lift but is highly flammable, making it unsuitable for most applications. Other gases, such as ammonia and methane, have been considered but present their own risks.
Helium’s safety and performance make it the standard choice for modern UAVs.
Advances in UAV Design and Research
Recent research has focused on improving the efficiency and control of hybrid UAVs. Computational Fluid Dynamics (CFD) simulations help engineers test new shapes and configurations. For example, studies have shown that V-shaped airships with aerofoil envelopes can achieve higher aerodynamic efficiency at greater speeds.
Adding wings to a conventional airship can triple the lift at positive angles of attack. However, this also increases drag, so designers must balance lift and efficiency. Adjusting the position and orientation of wings can also improve rolling stability.
Empennage design, or the shape of the tail, affects longitudinal stability. Studies show that a “+” type tail provides better static stability than an inverted “Y” type. These findings guide the development of safer and more manoeuvrable UAVs.
For more on UAV design principles, see the article on UAV propulsion systems at UKessays.com.
Materials and Manufacturing for UAV Manoeuvrability
The choice of materials is crucial for UAV performance. Lightweight, strong materials allow for greater payloads and better manoeuvrability. Modern UAVs use advanced composites, such as carbon fibre and thermoplastic polyurethane (TPU) films.
Envelope and Gondola Design
A typical UAV airship consists of two main parts: the envelope and the gondola. The envelope holds the lifting gas and provides aerodynamic shape. The gondola carries electronics, cameras, batteries, and propulsion systems.
Designers often build full-scale paper models before manufacturing the final product. This approach helps identify errors and ensures that all parts fit together. Once the design is tested, the final envelope is made from TPU film. This material is less rigid than paper and offers better durability.
Material Requirements
Materials used in UAVs must meet several key requirements:
- Low permeability to helium.
- High tear strength and damage tolerance.
- Resistance to temperature changes and humidity.
- Fatigue resistance for repeated inflation and deflation.
- Reliable joining techniques.
Meeting these requirements ensures that UAVs remain safe and effective during long missions.
UAV Control Systems and Propulsion
UAV manoeuvrability relies on precise control systems. Modern UAVs use a combination of propellers, control surfaces, and advanced electronics. These systems allow the UAV to adjust its position, speed, and orientation in real time.
Propulsion Options
Most UAVs use electric or internal combustion engines to drive their propellers. Electric motors are quiet and efficient, making them ideal for surveillance missions. Some UAVs use vectored thrust, which allows the direction of the thrust to change. This improves control during take-off, landing, and hovering.
Control Surfaces
Control surfaces, such as rudders and elevators, help steer the UAV. In hybrid designs, these surfaces work alongside vectored propellers to provide greater agility. Engineers use simulations and wind tunnel tests to optimise the placement and size of these surfaces.
Sensors and Autonomy
Modern UAVs are equipped with sensors for navigation, obstacle avoidance, and data collection. Autopilot systems use these sensors to maintain stable flight and execute complex manoeuvres. Advances in artificial intelligence have made UAVs more autonomous and responsive to changing conditions.
For more on the role of sensors in UAVs, see the article on sensor integration in UAVs at UKessays.com.
Comparing UAV Manoeuvrability: Airships vs. Drones
UAVs come in many forms, each with its own strengths and weaknesses. The table below compares key aspects of airship-based UAVs and multi-rotor drones.
Feature | Airship UAVs | Multi-rotor Drones |
---|---|---|
Endurance | High (hours to days) | Low (minutes to an hour) |
Payload Capacity | High | Moderate to low |
Manoeuvrability | Moderate | High |
Stability in Wind | Low to moderate | High (with advanced control) |
Take-off/Landing Space | Minimal (vertical possible) | Minimal (vertical) |
Noise Level | Low | Moderate to high |
Operating Cost | Low (helium cost) | Moderate (battery/maintenance) |
Airship UAVs excel in endurance and payload capacity. They can stay aloft for long periods and carry heavy equipment. However, they are more affected by wind and have slower response times. Multi-rotor drones are highly agile and can hover precisely, but their flight times are limited by battery life.
Challenges in UAV Manoeuvrability
Despite advances, UAVs still face several challenges:
- Wind and weather can destabilise lighter-than-air UAVs.
- Payload weight affects lift and manoeuvrability.
- Battery life limits the range of electric UAVs.
- Regulatory restrictions may limit where and how UAVs can fly.
Engineers continue to develop solutions to these problems. Improved materials, better batteries, and smarter control systems are making UAVs more reliable and versatile.
Future Trends in UAV Manoeuvrability
The future of UAVs lies in greater autonomy, improved materials, and hybrid designs. Researchers are exploring new ways to combine buoyancy, aerodynamic lift, and vectored thrust. These innovations promise UAVs that can handle a wider range of missions.
For example, swarming UAVs can work together to cover large areas or perform complex tasks. Advances in artificial intelligence will allow UAVs to adapt to changing environments in real time.
Hydrogen fuel cells and solar panels may extend flight times even further. New materials will reduce weight and increase durability. As a result, UAVs will become even more manoeuvrable and capable.
For a broader look at future UAV technologies, see the article on emerging UAV trends at UKessays.com.
Conclusion
UAV manoeuvrability has improved dramatically in recent years. Modern designs blend the best features of airships, aeroplanes, and helicopters. Advances in materials, control systems, and propulsion have made UAVs more agile, efficient, and reliable.
While challenges remain, ongoing research continues to push the boundaries of what UAVs can achieve. As technology advances, we can expect UAVs to play an even greater role in surveillance, transport, and disaster response.
For those interested in the technical and practical aspects of UAV design, further reading on UKessays.com provides valuable insights into propulsion, sensor integration, and future trends. These resources offer in-depth analysis and case studies to support your understanding of UAV manoeuvrability.
References to UAV Manoeuvrability
- Adamczyk G., 2017, Development of a Mini Airship for Surveillance and Terrain Mapping, School of Mechanical Civil and Aerospace Engineer, University of Manchester.
- Andan D., Asrar W., and Omar A. A., 2012, Aerodynamics of Hybrid Airship, Department of Mechanical, Kulliyyah of Engineering, International Islamic University Malaysia, pp. 154-161.
- Goodyear Aerospace Corp. [image], Contract NAS2-8643, 1975.
- Haque A., Asrar W., Omar A. A., Suleiman E., Ali J. M., 2014, Static Longitudinal Stability of a Hybrid Airship, Department of Mechanical Engineering, International Islamic University of Malaysia (IIUM), pp. 343-348.
- Haque A., Asrar W., Omar A. A., Suleiman E., Ali J. M., 2014, Stability and Take-off Ground Roll Issues of Hybrid Buoyant Aircraft, Department of Mechanical Engineering, International Islamic University of Malaysia (IIUM), pp. 504-507.
- Koury G. A., Gillett D., 1999, Airship Technology, Cambridge Aerospace Series 10.
- Livejournal, 2016, [image] Available at https://youroker.livejournal.com/58382.html [Accessed 5 Dec. 2018].
- Liu G., Wang F., Hong G., 2011, Dynamic Modeling and Dynamic Characteristic Analysis of a New Concept Stratospheric V-shaped Airship National Laboratory for Aeronautics and Astronautics, Beijing University of Aeronautics and Astronautics, pp. 37-42.
- Miller S., Fesen R., Hillenbrand L., Rhodes J., 2013 AIRSHIPS: A New Horizon for Science, The Keck Institute for Space Studies. [Online] Available at: kiss.caltech.edu/final_reports/Airship_final_report.pdf [Accessed 5 Dec. 2018].
- Motiwala N. I., Khan I. A, Yelve N. P., Narkhede, Pant R. S., 2013, Conceptual Approach for Design, Fabrication and Testing Remotely Controlled Airship, Dept of Aerospace Engg, Indian Institute of Technology Mumbai, India, pp 3390-3395.
- Pasternak I., Liao L., 2009, A review of airship structural research and development. Aeros Montbello USA.
- Pozdravish, 2011, [image] Available at: pozdravish.ru/wp content/uploads/2011/05/den_ispitaniya_parashuta_2.jpg [Accessed 5 Dec. 2018]
- Syon G., Time, 2017, Why the Hindenburg Disaster Is Still Worth Remembering. [image] Available at: https://time.com/4764799/hindenburg-disaster-80-years/ [Accessed 5 Dec. 2018]
Cite This Work
To export a reference to this article please select a referencing stye below:
Related Services
View allDMCA / Removal Request
If you are the original writer of this essay and no longer wish to have your work published on UKEssays.com then please click the following link to email our support team:
Request essay removal